Over 80 years of detailed experience: Hwacheon combines traditional craftsmanship with modern technology. Our expertise in machine tool manufacturing ensures high production quality and continuous innovation for future-proof concepts in the German market.
C2
Category
Multitasking LathesMachine series
C - BaureiheAvailable with
- Siemens 828D
- Fanuc 0i Plus
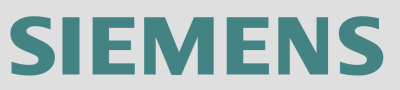
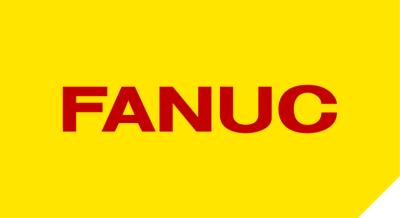
Size of C2
Chuck-Size | mm | 200 |
Max. cutting diameter | mm | 630 |
Swing over bed | mm | 730 |
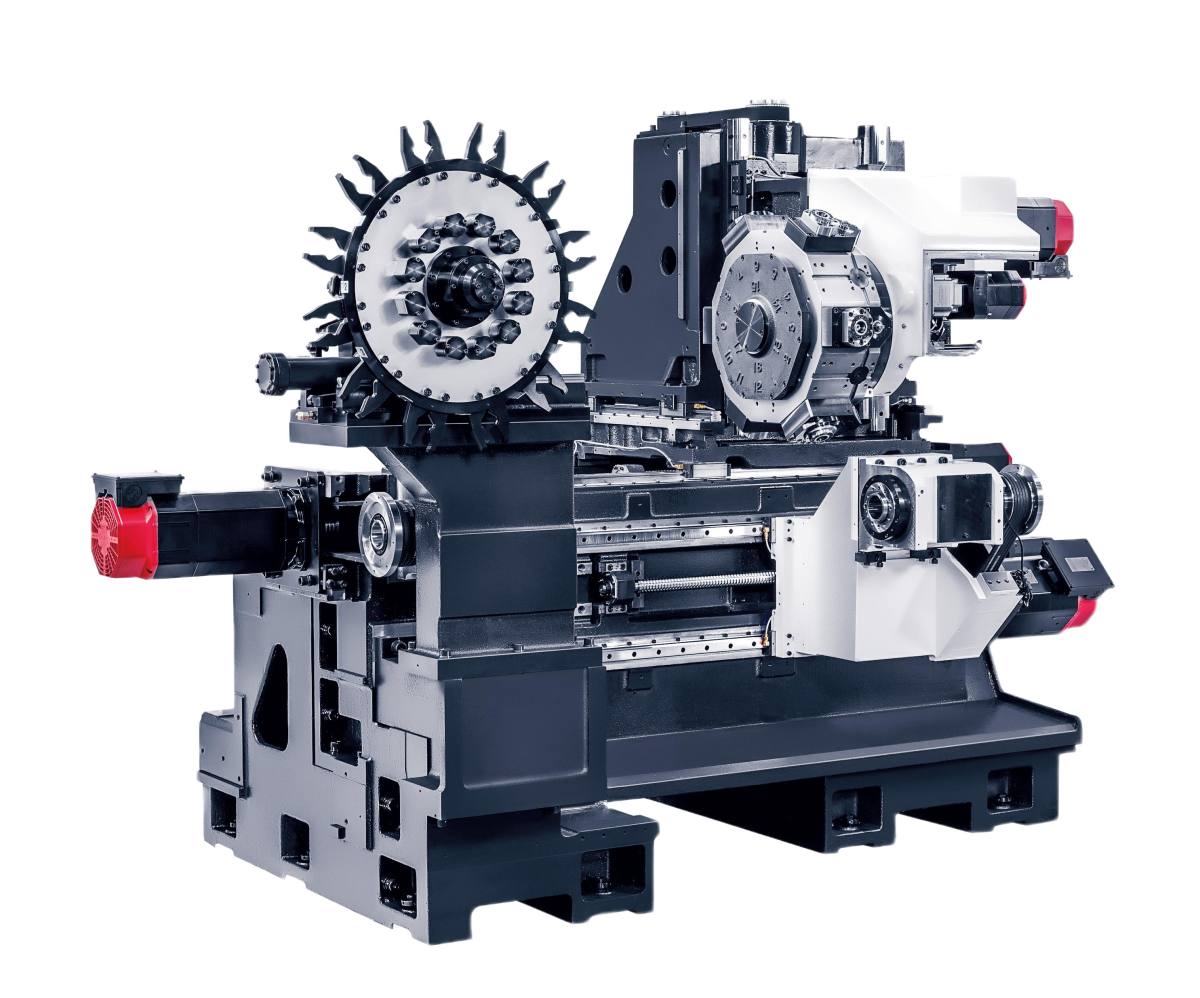
Tradition Meets Modernity
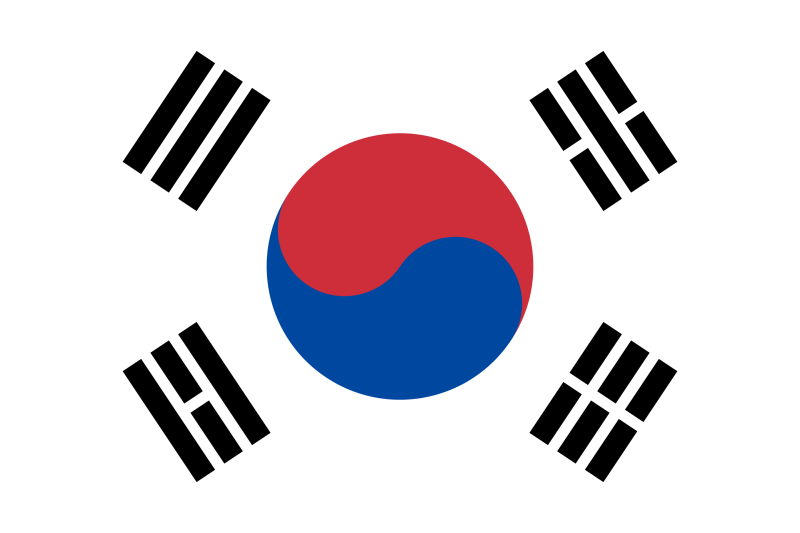
Dynamic Linear Guides
Speed and Dynamics Combined: Linear roller guides provide high dynamics and rapid traverse speeds. The workpiece weight is transferred linearly to the rollers, which must withstand enormous pressure at contact points. Therefore, we exclusively use linear roller guides from renowned manufacturers.
Why choose us?
Tradition Meets Modernity
Over 80 years of detailed experience: Hwacheon combines traditional craftsmanship with modern technology. Our expertise in machine tool manufacturing ensures high production quality and continuous innovation for future-proof concepts in the German market.
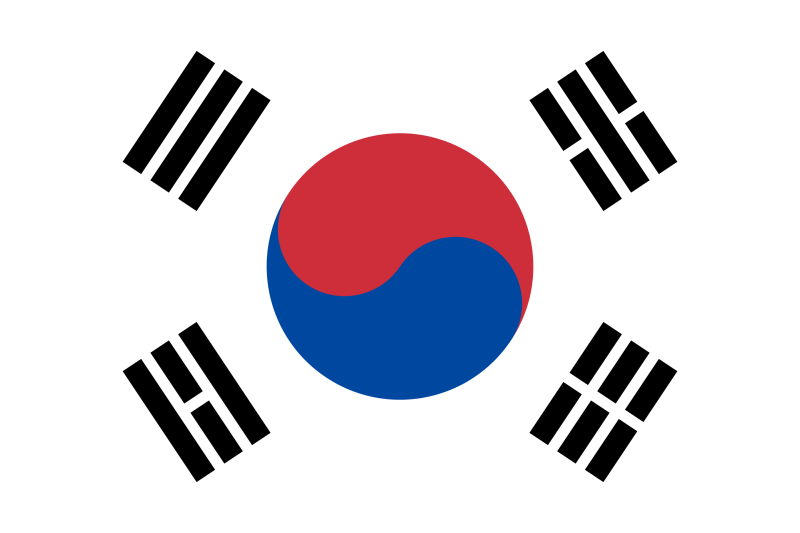
In-House Quality
Quality is created here: With our own manufacturing depth, including foundry and spindle production, we ensure durable and reliable machines. Quality and control go hand in hand to meet the German standards.
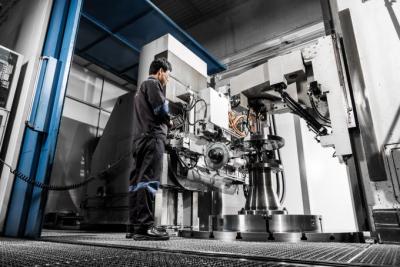
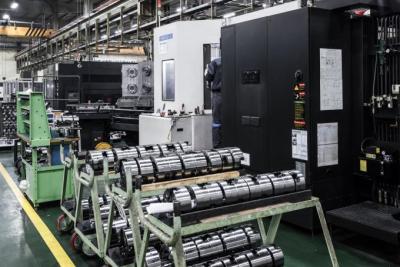
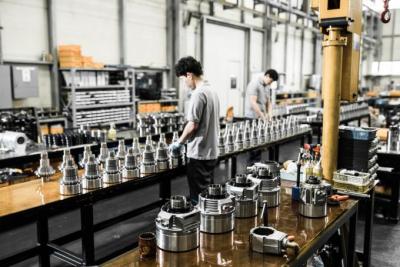
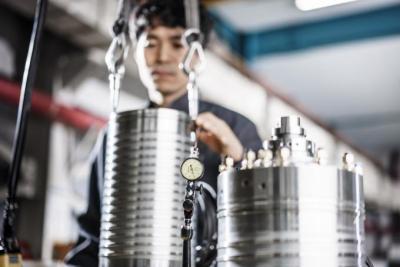
Technical Data
Item | Unit | C2 |
---|---|---|
Axis-Stroke (X / Y / Z) | mm | 360 / 120 / 700 |
Spindle power | kW | 15 / 11 |
Spindle speed | rpm | 5000 |
Rapid speed | m/min | 30 / 15 / 30 |
Tool shank | none | BMT-55 / C4 |
Number of tools | none | 18 + 12 |
Machine weight | kg | 10800 |
Max. cutting diameter | mm | 630 |
Max. cutting length | mm | 564 |
Chuck-Size | mm | 200 |
Swing over bed | mm | 730 |
Max. Bar size | mm | 65 |
Sub spindle speed | rpm | 6000 |
Sub spindle motor power | kW | 15 / 11 |
Coolant tank vol. | Liter | 230 |
Spindle torque | Nm | 477 / 233 |
Configurations
Y | MC | S | |
---|---|---|---|
C1 | Std. | Std. | Optional |
C2 | Std. | Std. | Optional |
Features of C2
Turret
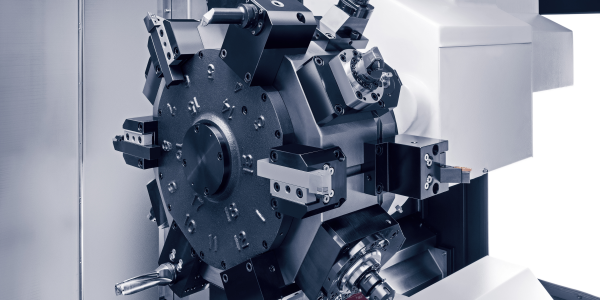
Number of tools | none | 18 + 12 |
Tool shank | none | BMT-55 / C4 |
Clamping Technology
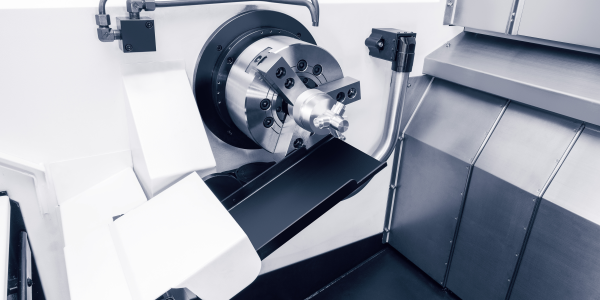
Chuck-Size | mm | 200 |
Fanuc 0i Plus
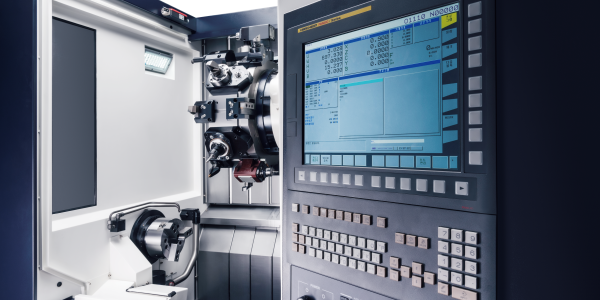
Automatic Tool Changer

Number of tools | none | 18 + 12 |
Tool shank | none | BMT-55 / C4 |
Workspace
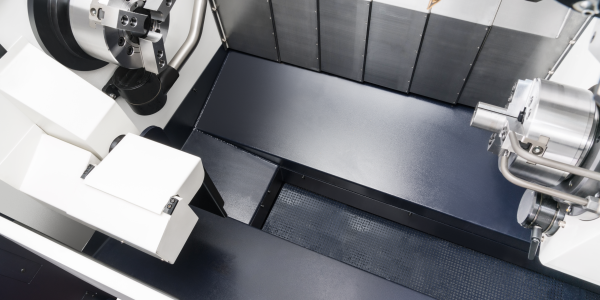
Tool measuring
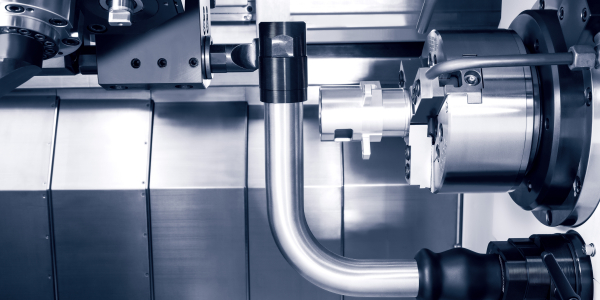
Peripherals and accessories
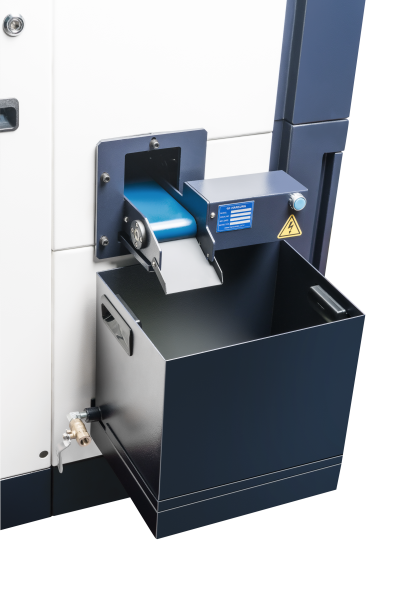
Y-Axis
Greater Flexibility and Time Savings: Lathes with a Y-axis enable 3-axis interpolation movements and the creation of off-center bores and milling operations. This allows workpieces to be fully machined in a single setup, eliminating operations on other machines and increasing machining accuracy. Additionally, they optimize grooving and parting processes by reducing lever forces for faster workflows.
- Axis-Stroke (X / Y / Z)360 / 120 / 700mm
Counter Spindle
Precision in Every Dimension: Lathes with a counter spindle enable back-side machining of workpieces and can alternatively be used as an NC tailstock. This back-side machining saves time and effort by eliminating the need for re-clamping on another machine. It also improves precision since the workpiece does not need realignment. For enhanced process stability and safe ejection of finished workpieces, optional pneumatic or mechanical ejectors and spindle flushing can be added.
- Sub spindle motor power15 / 11kW
- Sub spindle speed6000rpm
Driven Tools
Precision and Versatility Combined: Driven tools on lathes significantly expand machining capabilities. They enable milling, drilling, and other processes directly on the lathe, reducing re-clamping operations and minimizing downtime. Using various tools in a single setup increases machining accuracy and boosts overall productivity.
Steady Rest Carriage
Stability for Precise Results: The steady rest ensures maximum precision for long workpieces through optimal support. It reduces vibrations, improves surface quality, and enables precise machining even for demanding projects.
Dynamic Linear Guides
Speed and Dynamics Combined: Linear roller guides provide high dynamics and rapid traverse speeds. The workpiece weight is transferred linearly to the rollers, which must withstand enormous pressure at contact points. Therefore, we exclusively use linear roller guides from renowned manufacturers.
Internal Coolant Supply
ICS Makes the Difference!: The internal coolant supply (ICS) delivers coolant directly to the cutting edge, optimizing lubrication and chip removal. It boosts productivity, extends tool life, and enhances process reliability.
High-Quality Pretensioned Ball Screws
Thermal Stability for Precision and Reliability: Pretensioned ball screws reliably and stably compensate for thermal expansion. This technology prevents unwanted elongation of the spindles, ensuring lasting precision and consistently high machining accuracy over extended operating periods.
Automatic Workpiece Changer
Autonomy and Efficiency Maximized: Automatic workpiece changers extend a machine’s unmanned operating time by independently changing workpieces without operator intervention. This supports multi-machine operation, optimizes cost-effectiveness, and maximizes machine utilization during extended operating periods.
Excellent Chip Disposal
Perfect Chip Removal for Your Machine!: Our innovative chip disposal systems reliably remove chips, reduce heat, and optimize machining. High-quality components ensure uninterrupted operation and maximum process reliability.
- Coolant tank vol.230Liter
Other features and options
BMT-55 / VDI-30, Extra Tool Magazin, Belt-Driven Spindle, Tailstock, Parts catcher, Siemens 828D, Chip Conveyor, Work table, Machine SizeVideo gallery
Stock and Demonstration Machines
Hi-TECH 230
Hi-TECH 230AL YSMC (Fanuc)
Features and Options
Hi-TECH 230BL YSMC (Fanuc 0i Plus)
Features and Options
C1
Chuck-Size | mm | 200 |
Max. cutting diameter | mm | 630 |
Swing over bed | mm | 730 |
C2
Chuck-Size | mm | 200 |
Max. cutting diameter | mm | 630 |
Swing over bed | mm | 730 |