Robuste Drehzentren im Dauereinsatz
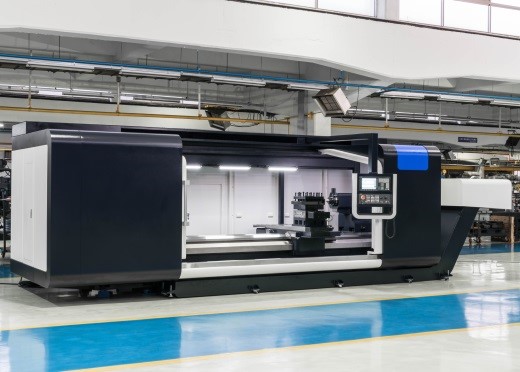
Zulieferbetriebe von Automobilherstellern müssen bei den oft in großen Stückzahlen gefertigten Bauteilen hohe Qualitätskriterien erfüllen. Gleichzeitig sollen in der Massenproduktion von Drehteilen die Bearbeitungszeiten pro Werkstück möglichst gering ausfallen. Hierzu werden Drehmaschinen benötigt, auf denen die zum Teil komplexen Werkstücke mit möglichst wenigen Aufspannungen fertig bearbeitet werden können. Der Premiumzulieferer Beinbauer Automotive aus dem niederbayerischen Büchlberg setzt zur Bearbeitung von Fahrwerksteilen für Nutzfahrzeuge seit über zehn Jahren erfolgreich auf robuste vertikale Drehzentren eines südkoreanischen Herstellers.
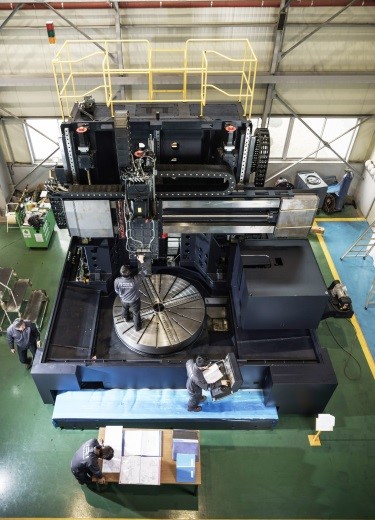
Am Ortsrand der beschaulichen Gemeinde Büchlberg im südlichen Bayerischen Wald liegen die Werkhallen der Beinbauer Automotive GmbH & Co. KG. Das Unternehmen gilt als größter Machining Service Provider in Westeuropa, der die Automobilindustrie und deren OEMs beliefert. An den drei Standorten Büchlberg, Obernzell und Patriching sind insgesamt 595 Mitarbeiter beschäftigt. Zur Bearbeitung kommen in erster Linie Guss- und Schmiedeteile, aber auch Werkstücke aus Aluminium. Vor allem Fahrgestellteile, Achsschenkel, Getriebegehäuse und Stabilisatoren werden in den Betrieben gefertigt. Neben der Produktion von einbaufertigen Komponenten und Baugruppen verfügt das Unternehmen über eine umfassende Logistikkompetenz und bietet den Auftraggebern eine Just-in-Time- bzw. Just-in-Sequence-Lieferung. Zu den Kunden zählen namhafte Hersteller von Nutzfahrzeugen, Landmaschinen, Pkws und Bahntechnik sowie deren Zulieferer.
Qualität auf allen Ebenen
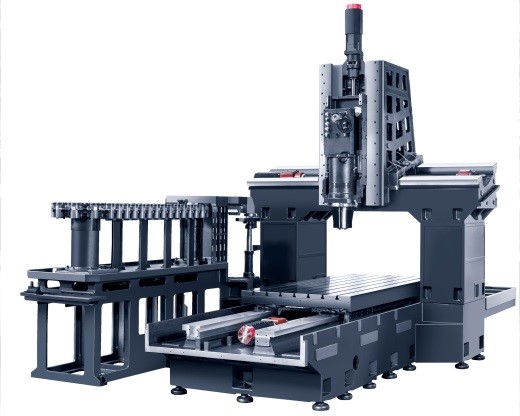
Um dem hohen Anspruch der Kunden gerecht zu werden, setzt das Unternehmen auf ein vorausschauendes und nachhaltiges Qualitätsmanagement. Zertifizierungen nach DIN ISO 9001:2008, ISO/TS 16949:2009, nach den Anforderungen des Kraftfahrt-Bundesamtes (KBA) und der Deutschen Bahn (HPQ) sowie nach herstellerbezogenen Produktqualifikationen sind Ausdruck der Qualitätsstrategie. Intern sorgen strenge Fehler-Reportings, umfassende Qualitätskontrollen und ein personenbezogenes Qualitäts-Commitment mit allen Mitarbeitern für maximale Qualitäts-, Kosten- und Terminsicherheit.
Auch sicherheitsrelevante Prüfungen werden hausintern durchgeführt. Dazu zählen beispielsweise Rissprüfungen an Stabilisatoren und Achsschenkeln, die einer 100%-Kontrolle unterzogen werden bevor sie das Werk verlassen. Für Drehteile stehen spezielle Prüflehren zur Verfügung, mit denen der Maschinenbediener direkt nach dem Bearbeitungsprozess relevante Durchmesser an den Werkstücken auf Maßhaltigkeit kontrolliert. Die Ergebnisse dieser Prüfungen werden in Messprotokollen dokumentiert und dem Kunden übermittelt. Dadurch kann dieser bei der Anlieferung der Teile auf die sonst übliche Wareneingangskontrolle verzichten und sie sofort in den weiteren Verarbeitungsprozess einschleusen, da Qualität und Fehlerfreiheit bereits nachgewiesen sind.
Stetiges Wachstum
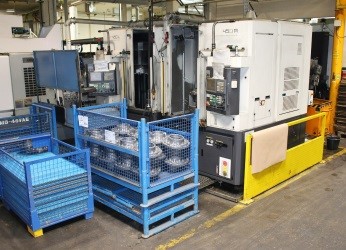
Seit fast 15 Jahren verzeichnet Beinbauer Automotive ein stetiges Umsatzwachstum. Auch die Zahl der Mitarbeiter hat sich von 238 im Jahr 2003 auf heute 595 mehr als verdoppelt. Dementsprechend ist ebenfalls in den Maschinenpark investiert worden, der kontinuierlich erneuert und erweitert wird. Aktuell sind an den drei Standorten insgesamt 220 Maschinen vorhanden, von denen 160 am Hauptsitz Büchlberg stehen.
Zur Betriebsausstattung gehören auch sieben Maschinen des südkoreanischen Werkzeugmaschinenherstellers Hwacheon. Dabei handelt es sich um besonders robuste horizontale und vertikale Drehzentren unterschiedlicher Baujahre. 2001 wurde die erste Maschine für Testläufe aufgestellt. Vier Jahre später folgten zwei horizontale Drehzentren Hi-Eco 31, die noch heute in Büchlberg im Einsatz sind. Auf ihnen werden beispielsweise Achsbrücken für Lkws bearbeitet.
Vollautomatische Fertigungszelle
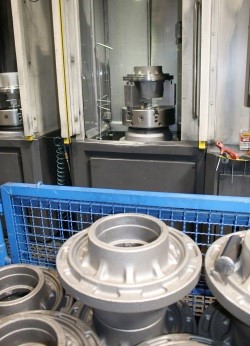
„Bei der Beschaffung war uns wichtig, dass die Maschinen über eine Niederdruckspannung am Drehfutter verfügen und die Maschinensteuerung eine Roboterschnittstelle hat“, sagt Christian Fuchs, Leiter Instandhaltung bei Beinbauer Automotive. „Darüber hinaus konnte uns auch das gute Preis-/Leistungsverhältnis der stabilen Maschinen überzeugen.“ Die VT-450-Drehzentren können wahlweise mit der Spindel an der linken oder an der rechten Seite geordert werden. In Obernzell wurden je eine linke und eine rechte Maschine verkettet. Auf der einen Maschine wird die Oberseite des Werkstücks bearbeitet, die andere übernimmt die Bearbeitung der Unterseite. Das Be- und Entladen sowie der Werkstückwechsel erfolgt über einen Roboter, so dass aus dieser Kombination zwischen Maschinen und Automatisierung eine vollautomatische Fertigungszelle entstanden ist.
Robuster Schichtbetrieb bei engsten Toleranzen
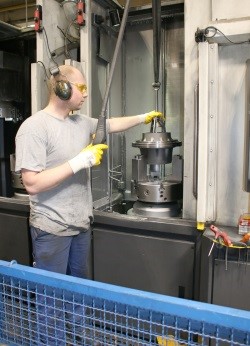
Im Hauptwerk Büchlberg sind fünf weitere VT-450 aus unterschiedlichen Baujahren im Einsatz. Trotz der harten Einsatzbedingungen sind Präzision und Zuverlässigkeit nach Angaben des Leiters Instandhaltung unverändert. Wie in Obernzell sind jeweils zwei Maschinen miteinander verkettet. Auf den Drehzentren werden u. a. Achsnaben, Ritzelgehäuse, Vorderrad-flansche oder Planetenträger gefertigt. Etwa 70 % der zu bearbeitenden Werkstücke bestehen aus Gusswerkstoffen, bei dem Rest handelt es sich um Schmiedeteile. Je nach Bauteil werden im Drei-Schicht-Betrieb bis zu 30.000 Stück pro Jahr bearbeitet. Die dabei einzuhaltenden Toleranzen liegen oft im Bereich von hundertstel Millimeter.
Bei den Maschinen in Büchlberg übernehmen die Bediener das Be- und Entladen sowie den Wechsel zwischen den Maschinen. Kleine Werkstücke werden von Hand umgespannt, während größere und schwere mittels Kran und einer speziellen Hebevorrichtung gehandhabt werden. Da bei der Bearbeitung von Werkstücken mit komplexen Geometrien nicht immer Standard-Spannbacken verwendet werden können, kommen hier häufig Sonderanfertigungen aus dem firmeneigenen Werkzeugbau zum Einsatz.
Vernetzte Produktion

Bei Beinbauer Automotive sind nicht nur die automatisierten Fertigungszellen vernetzt, hier ist man bereits seit mehreren Jahren in Richtung Industrie 4.0 unterwegs. „Sämtliche Maschinen sind über Schnittstellen mit einem eigenen Betriebsdatenerfassungs-System verbunden“, erklärt Christian Fuchs. „Hierüber werden alle wichtigen Maschinendaten erfasst und ausgewertet.“ Diese werden alle 90 Sekunden aktualisiert und an einen in der Instandhaltung stationierten Rechner übermittelt, der den aktuellen Status einer jeden Maschine visualisiert. Dabei ist den unterschiedlichen Betriebszuständen jeweils eine bestimmte Farbe zugeordnet, so dass Störungen schnell erkannt und zeitnah behoben werden können. Zusätzlich sind an allen Maschinen und Fertigungszellen Monitoren angebracht, auf denen auch die Bediener den aktuellen Zustand überwachen können. Die gesammelten Daten werden mit neuesten statistischen und AI-Verfahren ausgewertet. So bekommt die Instandhaltung schon frühzeitig Hinweise auf eventuelle Produktionsstörungen.
Deutschlandweites Service-Netzwerk
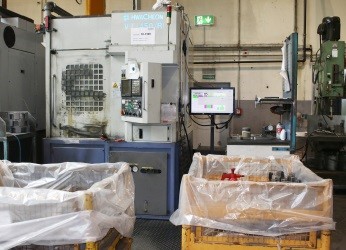
Damit auf kritische Betriebszustände schnell reagiert und ungeplante Stillstandzeiten minimiert werden können, erfolgen Wartung und Instandhaltung der Maschinen meistens durch das eigene Personal. Bisher musste erst einmal der Hwacheon-Kundendienst kontaktiert werden. „Ein nicht maßhaltiges Gussteil hatte an zwei Maschinen einen Crash verursacht“, erinnert sich Christian Fuchs. „Dabei wurden die Antriebsspindeln der Futter und die Linearführungen der Revolver schwer beschädigt.“ Für solche und ähnliche Fälle hält Hwacheon deutschlandweit ein regional strukturiertes Service-Netzwerk vor. Der Kundendienst wird dabei über die Service-Hotline in der Europa-Zentrale in Bochum angefordert. Diese übernimmt die weitere Koordination und schickt den nächstgelegenen Servicetechniker. Im Fall von Beinbauer Automotive konnten die kapitalen Schäden an den beiden Maschinen von der Begutachtung über die Demontage und Ersatzteilbeschaffung bis zur Instandsetzung innerhalb kürzester Zeit beseitigt und die damit verbundenen Stillstandzeiten gering gehalten werden.
Über 10 Jahre Dauerbetrieb
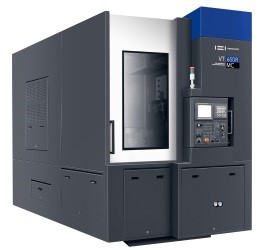
Ansonsten verrichten alle Hwacheon-Maschinen nach Angaben des Chef-Instandhalters zuverlässig und präzise ihren Dienst. Dabei sind sie erheblichen Belastungen ausgesetzt, da sie im Drei- bzw. Vierschichtbetrieb gefahren werden. Entsprechend überzeugt ist Christian Fuchs von der Robustheit und Langlebigkeit dieser Maschinen: „Eine Kombination aus zwei Drehzentren VT-450 ist bei uns über zehn Jahre lang rund um die Uhr, an 365 Tagen im Jahr, gelaufen und das ohne nennenswerte Stillstandzeiten.“ Umgerechnet hat jede der beiden Maschinen über diesen Zeitraum beeindruckende 87.600 Betriebsstunden geleistet. Bei einer durchschnittlichen Bearbeitungszeit von drei Minuten pro Teil sind dabei rund 1,7 Millionen Werkstücke präzise gefertigt worden.